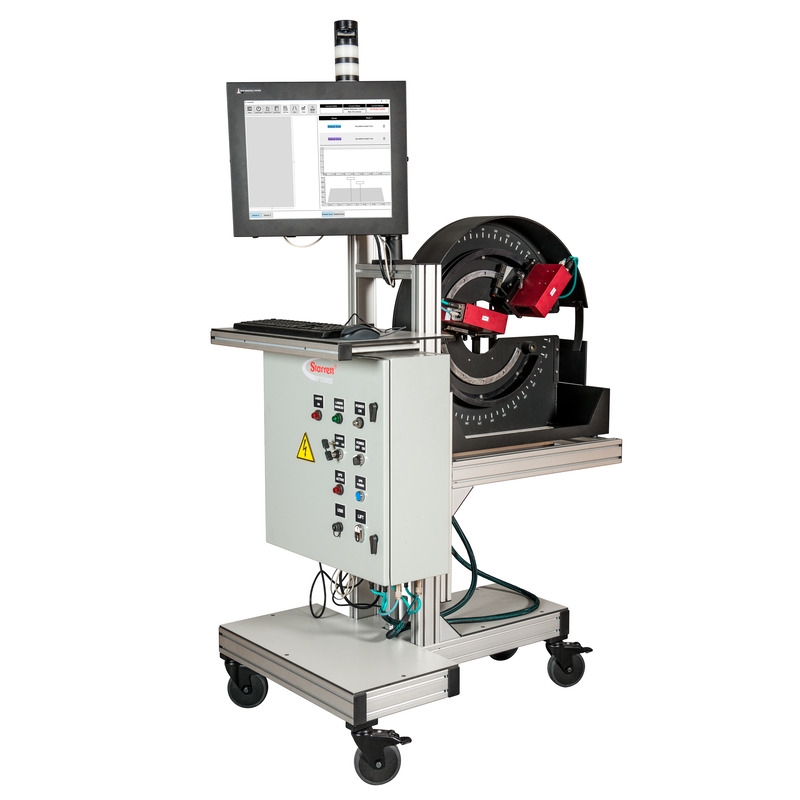
Surface360™
An inline inspection system that digitizes the extrusion and measures the true surface geometry in real-time.
Surface360™
Surface360™ from Starrett-Bytewise is a breakthrough in surface inspection technology. Surface360™ is an inline inspection system that digitizes the extrusion and measures the true surface geometry in real-time.
Surface360™ delivers an exciting alternative to existing technology. It is built upon the industry-leading high-speed laser triangulation capabilities of Starrett- Bytewise's profile measurement platform, Profile360™. Because most surface defects in extrusion are actually small deformations, indentions, or protrusions of the profile, the method used by Surface360™ results in more accurate detection of surface flaws.
FEATURES
- High-speed laser triangulation
- Inspects geometrical deviations
- View 3D image in real-time
- Detect flaws down to 0.5mm
TECHNOLOGY
- Surface360™ utilizes laser triangulation at rates 100x faster than traditional cross-section profile measurement systems to detect small changes in surface geometry
SOFTWARE
- Advanced software displays your extrusion in 3D view to highlight flaws
- Quickly scroll through a defect history of 3D images with timestamps
- Define size and frequency of defects that constitute a rule violation for alarming/marking
- Set boundaries for the flaw detection, avoiding non-critical surfaces
- Geometrical-matching overcomes challenges when the part moves or rotates within the field-of-view to maintain consistent inspection
- View reports with statistics on defects for past runs
- No calibration or "part mastering" required!
OUTPUTS
- Light Tower with audible alarm brings immediate attention to problems
- Micro PLC is included to tie to marking or reject system, so that flawed parts are not packaged for shipment
Our global team is standing by to help - Please contact us!
Related Information